Причины, особенности и методы защиты от электрохимической коррозии. Анодная защита. Использование пассивности в практике защиты от коррозии
Защита трубопроводов от коррозии может выполняться посредством множества технологий, наиболее эффективным из которых является электрохимический метод, к которому и относится катодная защита. Зачастую антикоррозийная катодная защита применяется комплексно, вместе с обработкой стальной конструкции изолирующими составами.
В данной статье рассмотрена электрохимическая защита трубопроводов и особенно детально изучен ее катодный подвид. Вы узнаете, в чем заключается суть данного метода, когда его можно использовать и какое оборудование применяется для катодной защиты металлов.
Cодержание статьи
Разновидности катодной защиты
Катодная защита стальных конструкций от коррозии была изобретена в 1820-х годах. Впервые метод был применен в кораблестроении — защитными анодными протекторами был обшит медный корпус судна, что значительно уменьшило скорость корродирования меди. Методика была взята на вооружение и начала активно развиваться, что сделало ее одним из наиболее эффективных методов противокоррозионной защиты на сегодняшний день.
Катодная защита металлов, согласно технологии выполнения, классифицируется на две разновидности:
- метод №1 — к защищающейся конструкции подсоединяется внешний источник тока, при наличии которого само металлическое изделие выполняется роль катода, тогда как в качестве анодов выступают сторонние инертные электроды.
- метод №2 — «гальваническая технология «: защищаемая конструкция контактирует с протекторной пластиной изготовленной из металла, имеющего больший электроотрицательный потенциал (к таким металлам относится цинк, алюминий, магний и их сплавы). Функцию анода в данном метода выполняют оба металла, тогда как электрохимическое растворение металла протекторной пластины обеспечивает протекание через защищаемую конструкцию необходимого минимума катодного тока. По истечению времени протекторная пластина полностью разрушается.
Метод №1 — наиболее распространенный. Это простая в реализации противокоррозионная технология, которая эффективно справляется с многими разновидностями коррозии металлов:
- межкристальная коррозия нержавеющей стали;
- питтинговая коррозия;
- растрескивание латуни из повышенного напряжения;
- коррозия под воздействием блуждающих токов.
В отличие от первого метода, пригодного для защиты больших по размеру конструкций (применяется для подземных и наземных трубопроводов), гальваническая электрохимзащита предназначена для применения с изделиями малых размеров.
Гальванический метод широко распространен в США, в России он практически не используется, поскольку технология возведения трубопроводов в нашей стране не предусматривает обработку магистралей специальным изоляционным покрытием, которое является обязательным условием для гальванической электрохимзащиты.
Отметим, что без значительно увеличивается коррозия стали под воздействием грунтовых вод, что особенно характерно для весеннего периода и осени. Зимой, после замерзания воды, коррозия от влаги существенно замедляется.
Суть технологии
Катодная противокоррозионная защита осуществляется посредством применения постоянного тока, который подается на защищаемую конструкцию от внешнего источника (чаще всего используются выпрямители, преобразующие переменный ток в постоянный) и делает ее потенциал отрицательным.
Сам объект, подключенный к постоянному току, является «минусом» — катодом, тогда как подведенное к нему анодное заземление, является «плюсом». Ключевым условием эффективности катодной защиты является наличие хорошо проводимой электролитической среды, в качестве которого при защите подземных трубопроводов выступает грунт, тогда как электронный контакт достигается за счет использования металлических материалов с высокой проводимостью.
В процессе реализации технологии между электролитической средой (грунтом) и объектом постоянно поддерживается требуемая разница потенциала тока, величина которой определяется с помощью высокоомного вольтметра.
Особенности катодной защиты трубопроводов
Коррозия — основная причина разгерметизации всех типов трубопроводов. Из-за повреждения металла ржавчиной на нем образуются разрывы, каверны и трещины, приводящие к разрушению стальной конструкции. Данная проблема особенно критична для подземных трубопроводов, которые постоянно пребывают в постоянном контакте с грунтовыми водами.
Катодная защита газопроводов от коррозии выполняется одним из вышеуказанных способов (посредством внешнего выпрямителя либо гальваническим методом). Технология в, данном случае, позволяет уменьшить скорость окисления и растворения металла, из которого изготовлен трубопровод, что достигается за счет смещения его естественного коррозийного потенциала в отрицательную сторону.
Посредством практический испытаний было выяснено, что потенциал катодной поляризации металлов, при котором замедляются все коррозийные процессы, равен -0.85 В , тогда как у подземных трубопроводов в естественном режиме он составляет -0.55 В.
Чтобы противокоррозионная защита было эффективной, необходимо посредством постоянного тока снизить катодный потенциал металла, из которого изготовлен трубопровод, на -0.3 В. В таком случае скорость корродирования стали не превышает 10 микрометров в течении года.
Катодная защита — наиболее эффективный метод защиты подземных трубопроводов от блуждающих токов. Под понятием блуждающих токов подразумевается электрический заряд, который попадает в землю в результате работы точек заземления ЛЭП, громоотводов либо движения поездов по железнодорожным магистралям. Точное время и место появления блуждающих токов выяснить невозможно.
Коррозийное воздействие блуждающих токов на металл происходит в случае, если металлическая конструкция имеет позитивный потенциал относительно электролита(для подземных трубопроводов электролитом выступает грунт). Катодная защита же делает потенциал металла подземных трубопроводов отрицательным, что устраняет риск их окисления под воздействием блуждающих токов.
Технология применения внешнего источника тока для катодной защиты подземных трубопроводов предпочтительна. Ее преимущества — неограниченный энергоресурс, способный преодолевать удельное сопротивление грунта.
В качестве источника тока противокоррозионная защита используется воздушные линии электропередач мощностью 6 и 10 кВт, если же на территории ЛЭП отсутствуют, могут применяться мобильные генераторы, работающие на газу и дизтопливе.
Детальный обзор технологии катодной защиты от коррозии (видео)
Оборудование для катодной защиты
Для противокоррозионной защиты подземных трубопроводов применяется специальное оборудование — станции катодной защиты (СКЗ), состоящие из следующих узлов:
- заземление (анод);
- источник постоянного тока;
- пункт управления, контроля и измерений;
- соединительные кабели и провода.
Одна СКЗ, подключенная к электросети либо к автономному генератору, может выполнять катодную защиту сразу нескольких рядом расположенных магистралей подземных трубопроводов. Регулировка тока может выполняться вручную (посредством замены обмотки на трансформаторе) либо в автоматическом режиме (если система укомплектована тиристорами).
Среди станций катодной защиты, применяемых в отечественной промышленности, наиболее технологичной установкой считается Минерва-3000 (спроектированная инженерами из Франции по заказу Газпрома). Мощности данной СКЗ достаточно для эффективной защиты 30 км подземного трубопровода.
К преимуществам установки относится:
- повышенная мощность;
- функция восстановления после перегрузок (обновление происходит за 15 секунд);
- наличие систем цифрового регулирования для контроля за рабочими режимами;
- полная герметичность ответственных узлов;
- возможность подключения оборудования для удаленного контроля.
Также широко востребованными в отечественном строительстве являются установки АСКГ-ТМ, в сравнении с Минервой-3000 они имеют уменьшенную мощность (1-5 кВт), однако в стоковой комплектации система оборудована телеметрическим комплексом, который в автоматическом режиме контролирует работу СКЗ и имеет возможность дистанционного управления.
Станции катодной защиты Минерва-3000 и АСКГ-ТМ требуют питания от электросети мощностью 220 В. Удаленное управление оборудованием выполняется посредством встроенных GPRS модулей. СКЗ имеют достаточно больше габариты — 50*40*90 см. и вес — 50 кг. Минимальный срок службы устройств составляет 20 лет.
До сих пор при обустройстве протяжённых промышленных трубопроводов наиболее востребованным материалом изготовления труб является сталь. Обладая множеством замечательных свойств, таких как механическая прочность, способность функционировать при больших значениях внутренних давления и температуры и стойкость к сезонным изменениям погоды, сталь имеет и серьёзный недостаток: склонность к коррозии, приводящей к разрушению изделия и, соответственно, неработоспособности всей системы.
Один из способов защиты от этой угрозы – электрохимический, включающий катодную и анодную защиту трубопроводов; об особенностях и разновидностях катодной защиты будет рассказано ниже.
Определение электрохимической защиты
Электрохимическая защита трубопроводов от коррозии – процесс, осуществляемый при воздействии постоянного электрического поля на предохраняемый объект из металлов или сплавов. Поскольку обычно доступен для работы переменный ток, используются специальные выпрямители для преобразования его в постоянный.
В случае катодной защиты трубопроводов защищаемый объект путём подачи на него электромагнитного поля приобретает отрицательный потенциал, то есть делается катодом.
Соответственно, если ограждаемый от коррозии отрезок трубы становится «минусом», то заземление, подводящееся к нему, – «плюсом» (т.е. анодом).
Антикоррозионная защита по такой методике невозможна без присутствия электролитической, с хорошей проводимостью, среды. В случае обустройства трубопроводов под землёй её функцию выполняет грунт. Контакт же электродов обеспечивается путём применения хорошо проводящих электрический ток элементов из металлов и сплавов.
В ходе протекания процесса между средой-электролитом (в данном случае грунтом) и защищаемым от коррозии элементом возникает постоянная разница потенциалов, значение которой контролируется при помощи высоковольтных вольтметров.
Классификация методик электрохимической катодной защиты
Такой способ предупреждения коррозии был предложен в 20-х годах XIX века и поначалу использовался в судостроении: медные корпуса кораблей обшивались протекторами-анодами, значительно снижающими скорость корродирования металла.
После того, как была установлена эффективность новой технологии, изобретение стало активно применяться в других областях промышленности. Через некоторое время оно было признано одним из самых эффективных способов защиты металлов.
В настоящее время используется два основных типа катодной защиты трубопроводов от коррозии:
- Самый простой способ : к металлическому изделию, требующему предохранения от коррозии, подводится внешний источник электрического тока. В таком исполнении сама деталь приобретает отрицательный заряд и становится катодом, роль же анода выполняют инертные, не зависящие от конструкции, электроды.
- Гальванический метод . Нуждающаяся в защите деталь соприкасается с защитной (протекторной) пластиной, изготавливаемой из металлов с большими значениями отрицательного электрического потенциала: алюминия, магния, цинка и их сплавов. Анодами в этом случае становятся оба металлических элемента, а медленное электрохимическое разрушение пластины-протектора гарантирует поддержание в стальном изделии требуемого катодного тока. Через более или менее долгое время, в зависимости от параметров пластины, она растворяется полностью.
Характеристики первого метода
Этот способ ЭХЗ трубопроводов, в силу простоты, наиболее распространён. Применятся он для предохранения крупных конструкций и элементов, в частности, трубопроводов подземного и наземного типов.
Методика помогает противостоять:
- питтинговой коррозии;
- коррозии из-за присутствия в зоне расположения элемента блуждающих токов;
- коррозии нержавеющей стали межкристального типа;
- растрескиванию латунных элементов вследствие повышенного напряжения.
Характеристики второго метода
Эта технология предназначается, в отличие от первой, в том числе для защиты изделий небольших размеров. Методика наиболее популярна в США, в то время как в Российской Федерации используется редко. Причина в том, что для проведения гальванической электрохимическая защита трубопроводов необходимо наличие на изделии изоляционного покрытия, а в России магистральные трубопроводы таким образом не обрабатываются.
Особенности ЭХЗ трубопроводов
Главной причиной выхода трубопроводов из строя (частичной разгерметизации или полного разрушения отдельных элементов) является коррозия металла. В результате образования на поверхности изделия ржавчины на его поверхности появляются микроразрывы, раковины (каверны) и трещины, постепенно приводящие к выходу системы из строя. Особенно эта проблема актуальна для труб, пролегающих под землёй и всё время соприкасающихся с грунтовыми водами.
Принцип действия катодной защиты трубопроводов от коррозии предполагает создание разности электрических потенциалов и реализуется двумя вышеописанными способами.
После проведения измерений на местности было установлено, что необходимый потенциал, при котором замедляется любой коррозионный процесс, составляет –0,85 В; у находящихся же под слоем земли элементов трубопровода его естественное значение равно –0,55 В.
Чтобы существенно замедлить процессы разрушения материалов, нужно добиться снижения катодного потенциала защищаемой детали на 0,3 В. Если добиться этого, скорость коррозии стальных элементов не будет превышать значений 10 мкм/год.
Одну из самых серьёзных угроз металлическим изделиям представляют блуждающие токи, то есть электрические разряды, проникающие в грунт вследствие работы заземлений линий энергопередачи (ЛЭП), громоотводов или передвижения по рельсам поездов. Невозможно определить, в какое время и где они проявятся.
Разрушающее воздействие блуждающих токов на стальные элементы конструкций проявляется, когда эти детали обладают положительным электрическим потенциалом относительно электролитической среды (в случае трубопроводов – грунта). Катодная методика сообщает защищаемому изделию отрицательный потенциал, в результате чего опасность коррозии из-за этого фактора исключается.
Оптимальным способом обеспечения контура электрическим током является использование внешнего источника энергии: он гарантирует подачу напряжения, достаточного для «пробивания» удельного сопротивления грунта.
Обычно в роли такого источника выступают воздушные линии энергопередачи с мощностями 6 и 10 кВт. В случае отсутствия на участке пролегания трубопровода ЛЭП следует использовать генераторы мобильного типа, функционирующие на газе и дизельном топливе.
Что нужно для катодной электрохимической защиты
Для обеспечения снижения коррозии на участках пролегания трубопроводов используются особые приспособления, называемые станциями катодной защиты (СКЗ).
Эти станции включают в себя следующие элементы:
- заземление, выступающее в роли анода;
- генератор постоянного тока;
- пункт контроля, измерений и управления процессом;
- соединительные приспособления (провода и кабели).
Станции катодной защиты вполне эффективно выполняют основную функцию, при подключении к независимому генератору или ЛЭП защищая одновременно несколько расположенных поблизости участков трубопроводов.
Регулировать параметры тока можно как вручную (заменяя трансформаторные обмотки), так и в автоматизированном режиме (в случае, когда в контуре имеются тиристоры).
Наиболее совершенной среди применяемых на территории РФ станций катодной защиты признаётся «Минерва-3000» (проект СКЗ по заказу «Газпрома» был создан французскими инженерами). Одна такая станция позволяет обеспечить безопасность около 30 км пролегающего под землей трубопровода.
Плюсы «Минервы-3000»:
- высокий уровень мощности;
- возможность быстрого восстановления после возникновения перегрузок (не более 15 секунд);
- оснащённость необходимыми для контроля рабочих режимов узлами цифровой регулировки системы;
- абсолютно герметичные ответственные узлы;
- возможность контролировать функционирование установки удалённо, при подключении специального оборудования.
Вторая наиболее популярная в России СКЗ – «АСКГ-ТМ» (адаптивная телемеханизированная станция катодной защиты). Мощность таких станций меньше, чем упомянутых выше (от 1 до 5 кВт), но их возможности автоматического контроля работы улучшены за счёт наличия в исходной комплектации телеметрического комплекса с дистанционным управлением.
Обе станции требуют источника напряжения мощностью 220 В, управляются с помощью модулей GPRS и характеризуются достаточно скромными габаритами - 500×400×900 мм при весе 50 кг. Срок эксплуатации СКЗ – от 20 лет.
Протекторная защита трубопроводов и других металлических изделий от коррозии представляет собой один из вариантов предохранения разнообразных конструкций от негативных коррозионных явлений.
1 Суть протекторной защиты металлов от коррозии
Данная подразумевает присоединение к предохраняемой металлической поверхности специального протектора – металла с более электроотрицательными характеристиками. При растворении под действием воздуха такой протектор начинает выполнять свою функцию, которая состоит в предохранении основного изделия от разрушения.
По сути, протекторная защита трубопроводов и иных магистралей от коррозии является одним из видов катодной электрохимической методики.
Описываемый способ антикоррозионной обработки оптимален для ситуаций, когда у предприятия нет возможности возвести специальные электрические линии для организации эффективной катодной защиты от либо их строительство признается экономически нецелесообразным. Протектор полностью выполняет свои задачи при условии, что величина переходного сопротивления между средой, окружающей обрабатываемый объект, и этим самым объектом невелика.
Протекторная защита изделий из металла от коррозии является результативной лишь на каком-либо конкретном расстоянии. Для того, чтобы установить данное расстояние, вводится понятие радиуса антикоррозионного действия используемого протектора. Он указывает на наибольшее удаление металла-защитника от предохраняемой конструкции.
Сущность коррозии металлов такова, что менее активный из них при взаимодействии станет присоединять к своим ионам электроны более активного, которые будут производиться активным компонентом системы. В результате происходит сразу два одновременных процесса:
- восстановление менее активного металла (он является катодом);
- окисление менее активного металла-анода, благодаря чему и происходит антикоррозионная защита газопровода, иной магистральной сети, какой-либо металлоконструкции.
Через определенное время действие протектора заканчивается (из-за утраты контакта с предохраняемым металлом либо при полном растворении "защитника"), после чего потребуется выполнить его замену.
2 Антикоррозионная защита при помощи протекторов – особенности методики
Применение протекторной защиты от коррозии трубопроводов и конструкций из металла в кислых средах не имеет смысла, что обусловлено повышенным темпом саморастворения протектора. Она рекомендуется для использования в нейтральных средах, будь то обычный грунт, речная или морская вода.
По отношению к железу более активными являются следующие металлы – магний, хром, кадмий, цинк и некоторые другие. Теоретически именно их следует применять для защиты газопровода либо другой конструкции. Но здесь имеется ряд нюансов, которые обуславливают технологическую нецелесообразность использования чистых металлов в качестве "защитников".
Магний в чистом виде, например, характеризуется повышенной скоростью собственного ржавления, на алюминии очень быстро появляется оксидная толстая пленка, а цинк без каких-либо примесей ввиду своей дендритной крупнозернистой структуры имеет свойство растворяться крайне неравномерно. Чтобы нивелировать все эти негативные явления, в чистые металлы, предназначенные для защиты трубопроводов и металлоконструкций от коррозии, добавляют легирующие компоненты. Другими словами, антикоррозионная защита, например, газопровода, подземного резервуара в большинстве случаев выполняется при помощи различных сплавов.
Часто используются сплавы на основе магния. В них вводят алюминий (от 5 до 7 процентов) и цинк (от 2 до 5 процентов), а также незначительные количества (буквально сотые либо десятые доли) никеля, свинца, меди. Защита от коррозии магниевыми сплавами применяется тогда, когда конструкция из металла (элементы трубопроводов, газопровода и так далее) функционирует в средах с показателем рН не более 10,5 (обычный грунт, водоемы с пресной или слабосоленой водой).
Такое ограничение связано с тем, что магний сначала очень быстро растворяется, а затем на его поверхности формируются соединения, характеризуемые затрудненным растворением. Стоит сказать отдельно об опасности использования магниевых композиций для защиты от коррозии – они могут стать причиной растрескивания изделий из металла, а также их охрупчивания (водородного).
Для металлоконструкций, установленных в соленой воде, газопровода, проложенного по морскому дну, рекомендуется использование протекторов на базе цинка, которые содержат:
- кадмий (от 0,025 до 0,15 %);
- алюминий (не более 0,5 %);
- медь, свинец, железо (от 0,001 до 0,005 % в сумме).
Протекторная защита трубопроводов в морской воде цинковыми составами будет гарантированно эффективной и длительной. Если же такие протекторы применять в грунте или пресных водоемах, они практически мгновенно покрываются гидроксидами и оксидами, что сводит на нет все антикоррозионные мероприятия.
А вот в соленой проточной воде, на прибрежном морском шельфе обычно эксплуатируются алюминиевые защитники от коррозии. В них содержится таллий, кадмий, кремний, индий (суммарно до 0,02 %), магний (не более 5 %) и цинк (не более 8 %). Данный состав не дает возможности появляться на алюминии окислам. Протекторная защита из алюминиевых составов используется в тех же условиях, что и из магниевых.
Цинковые протекторы обычно применяются для антикоррозионной защиты тех металлоконструкций, для которых должна быть обеспечена максимальная пожарная и взрывобезопасность (в частности, разнообразных трубопроводов для транспортировки потенциально горючих материалов, например, газопровода). Также цинковые защитные композиции не создают при анодном растворении загрязняющих соединений. За счет этого им практически нет замены, когда речь идет о защите от коррозии трубопроводов, по которым перемещают нефть, а также нефтеналивных и грузовых судов и танкеров.
3 Совместное применение лакокрасочных составов и протекторов
Нередко защита нефте- либо газопровода, той или иной конструкции из металла от коррозионных проявлений выполняется комбинацией протекторной и лакокрасочной защиты. Последняя по своей сути причисляется к пассивному методу предохранения от коррозии. По-настоящему высоких результатов она не обеспечивает, но зато позволяет в сочетании с протектором:
- нивелировать возможные изъяны покрытия трубопроводов и металлических конструкций, которые возникают по естественным причинам (отслаивание металла, его вспучивание, набухание, появление трещин и так далее), а также при их использовании (нет такого газопровода или танкера, покрытие которого в процессе эксплуатации не претерпевает определенных изменений);
- снизить (иногда весьма существенно) расход достаточно дорогостоящих протекторных материалов, повысив при этом их эксплуатационный срок;
- обеспечить распределение по металлической поверхности трубопроводов защитного тока максимально однородно (равномерно).
Добавим, что лакокрасочные слои во многих случаях довольно-таки сложно нанести на некоторые участки уже функционирующего резервуара, газопровода или водного судна. Тогда лучше, конечно же, не усложнять процесс и применять исключительно протекторы.
Анодную защиту применяют при эксплуатации оборудования в хорошо электропроводных средах и изготовленного из легко пассивирующихся материалов - углеродистых, низколегированных нержавеющих сталей, титана, высоколегированных сплавов на основе железа. Анодная защита перспективна в случае оборудования, изготовленного из разнородных пассивирующихся материалов, например, нержавеющих сталей различного состава, сварных соединений.
При анодной защите потенциал активно растворяющегося металла смещают в положительную сторону до достижения устойчивого пассивного состояния (рис. 10.1). В результате происходит не только существенное (в тысячи раз) снижение скорости коррозии металла, но и предотвращается попадание продуктов его растворения в производимый продукт. Смещение потенциала в положительную сторону можно осуществлять от внешнего источника тока, введением окислителей в раствор или введением в сплав элементов, способствующих повышению эффективности протекающего на поверхности металла катодного процесса.
Анодная защита пассивирующими ингибиторами-окислителями основана на том, что в процессе их восстановления возникает ток, до статочный для перевода металла в пассивное состояние. В качестве ингибиторов могут быть использованы соли нитраты, бихроматы и др. Применение ингибиторов позволяет защищать металл в труднодоступных местах - щелях, зазорах. Недостатком этого способа защиты является загрязнение технологической среды.
Без окислителей поляризовали потенциостатическим методом. Данные обоих опытов совпали. Это свидетельствует о том, что как при химической, так и при электрохимической обработке пассивное состояние металла определяется величиной потенциала, независимо от способа его достижения.
При анодной защите методом катодного легирования в сплав вводят добавки (чаще благородный металл), на котором катодные реакции восстановления деполяризаторов осуществляются с меньшим перенапряжением, чем на основном металле. Например, как было показано ранее, в сплавах титана с небольшим количеством палладия происходит селективное растворение титана, а поверхность непрерывно обогащается палладием. Палладий выступает как протектор и пассивирует сплав. Аналогичный эффект наблюдается и для хромистых сталей при введении в сплав благородных металлов.
Анодная защита от внешнего источника основана на пропускании тока через защищаемый объект и на смещении потенциала коррозии в сторону более положительных значений.
Установка для анодной защиты состоит из объекта защиты, катода, электрода сравнения и источника электрического тока.
при плотности тока растворения металла не более (1,5-Основным критерием, характеризующим состояние поверхности металла, является электродный потенциал. Обычно возможность применения анодной защиты для конкретного металла или сплава определяют методом снятия анодных поляризационных кривых. При этом получают следующие данные:
потенциал коррозии металла в исследуемом растворе;
протяженность области устойчивой пассивности;
Плотность тока в области устойчивой пассивности. Эффективность защиты определяют как отношение скорости коррозии без защиты к скорости коррозии под защитой.
Как правило, параметры анодной защиты, полученные в лабораторных и производственных условиях, хорошо согласуются между собой. В зависимости от конкретных условий эксплуатации область защитных потенциалов при анодной защите лежит на 0,3-1,5 В положительнее потенциала свободной коррозии, а скорость растворения металлов при этом может уменьшится в тысячи раз.
предотвращает образование питтингов и снижает скорость растворения стали в 2000 раз. В ряде случаев вследствие повышенной опасности возникновения локальных коррозионных процессов применение анодной защиты неэффективно. Резкий рост критического тока пассивации металлов с увеличением температуры агрессивных сред ограничивает применение анодной защиты в условиях повышенных температур.
При стационарном режиме работы установки величина тока поляризации, требуемого для поддержания устойчивого пассивного состояния, постоянно меняется вследствие изменения эксплуатационных параметров коррозионной среды (температуры, химического состава, условий перемешивания, скорости движения раствора и др.). Поддерживать потенциал металлоконструкции в заданных границах можно путем постоянной или периодической поляризации. В случае периодической поляризации включение и выключение тока производят либо при достижении определенного значения потенциала, либо при его отклонении на определенную величину. В обоих случаях параметры анодной защиты определяют опытным способом в лабораторных условиях.
В качестве катодов используют малорастворимые материалы, например, Рг, Та, РЬ, Ni, платинированную латунь, высоколегированные нержавеющие стали и др. Схема расположения катодов проектируется индивидуально для каждого конкретного случая защиты.
Для успешного применения анодной защиты объект должен отвечать следующим требованиям:
материал аппарата должен пассивироваться в технологической среде;
конструкция аппарата не должна иметь заклепок, количество щелей и воздушных карманов должно быть минимальным, сварка должна быть качественной;
катод и электрод сравнения в защищаемом устройстве должны постоянно находится в растворе.
В химической промышленности для анодной защиты наиболее пригодны аппараты цилиндрической формы, а также теплообменники. В настоящее время анодная защита нержавеющих сталей применяется для мерников, сборников, цистерн, хранилищ в производстве серной кислоты, минеральных удобрений, аммиачных растворов. Описаны случаи применения анодной защиты теплообменной аппаратуры в производствах серной кислоты и искусственного волокна, а также ванн для химического никелирования.
Анодная защита. Использование пассивности в практике защиты от коррозии.
Многие металлы находятся в пассивном состоянии в некоторых агрессивных средах. Хром, никель, титан, цирконий легко переходят в пассивное состояние и устойчиво его сохраняют. Часто легирование металла, менее склонного к пассивации, металлом, пассивирующем легче, приводит к образованию достаточно хорошо пассивирующихся сплавов. Примером могут служить разновидности сплавов Fе-Сr, представляющие собой различные нержавеющие и кислотоупорные стали, стойкие, например, в пресной воде, атмосфере, азотной кислоте и т.д. Подобное использование пассивности в технике защиты от коррозии известно давно и имеет огромное практическое значение. Но в последнее время возникло новое направление защиты металлов в таких окислителях, которые сами по себе не способны вызывать пассивность. Известно, что смещение потенциала активного металла в отрицательную сторону должно уменьшить скорость коррозии. Если потенциал становится отрицательнее равновесного в данной среде, то скорость коррозии должна стать равной нулю (катодная защита, применение протекторов). Очевидно, что подобным же образом, но за счет анодной поляризации от внешнего источника электрической энергии можно перевести способный к этому металл в пассивное состояние и тем уменьшить скорость коррозии на несколько порядков. Расход электрической энергии не должен быть велик, так как сила тока вообще весьма мала. Существуют требования, которым должна удовлетворять система, чтобы к ней можно было применить анодную защиту. Прежде всего, нужно надежно знать анодную поляризационную кривую для выбранного металла в данной агрессивной среде. Чем выше i п , тем большая сила тока потребуется для перевода металла в пассивное состояние; чем меньше i nn , тем меньший расход энергии потребуется для поддержания пассивности; чем шире диапазон Δφ n , тем большие колебания потенциала можно допустить, т.е. тем легче поддерживать металл в пассивном состоянии. Нужна уверенность в том, что в области Δφ n металл корродирует равномерно. В противном случае, даже при малой величине i nn возможно образование язв и сквозного разъедания стенки изделия. Форма защищаемой поверхности может быть довольно сложной, что затрудняет поддержание одинакового значения потенциала на всей поверхности; в этом отношении большая величина Δφ n особенно желательна. Конечно, требуется и достаточно хорошая электропроводность среды. Применение анодной защиты целесообразно в сильно агрессивных средах, например в химической промышленности. При наличие поверхности раздела жидкость-газ необходимо иметь в виду, что анодная защита не может распространяться на поверхность металла в газовой среде, что впрочем типично и для катодной зашиты. Если газовая фаза тоже агрессивна или имеется неспокойная поверхность раздела, что приводит к разбрызгиванию жидкости и оседанию капель ее на металл выше поверхности раздела, если происходит периодическое смачивание стенки изделия в определенной зоне, то приходится ставить вопрос об иных способах защиты поверхности выше постоянного уровня жидкости. Анодная защита может осуществляться несколькими способами. 1. Простое наложение постоянной э.д.с. от постороннего источника электрической энергии. Положительный полюс подключается к защищаемому изделию, а около его поверхности помещают катоды сравнительно малого размера. Они размещаются в таком количестве и на таком расстоянии от защищаемой поверхности, чтобы обеспечить по возможности равномерную анодную поляризацию изделия. Этот способ применяется в том случае, если Δφ n достаточно велик и нет опасности, при некоторой неизбежной неравномерности распределения потенциала анода, активации или перепассивации, т.е. выхода за пределы Δφ n . Таким способом можно защищать изделия из титана или циркония в серной кислоте. Нужно только помнить, что для пассивации сначала потребуется пропускание тока большей силы, что связано с переводом потенциала за φ n . Для начального периода целесообразно иметь дополнительный источник энергии. Следует учитывать также большую поляризацию катодов, плотность тока на которых велика вследствие их малых размеров. Однако, если область пассивного состояния велика, то изменение потенциала катода даже на несколько десятых вольта не представляет опасности. Периодическое включение и выключение тока защиты, когда изделие уже запассивировано. При включение анодного тока потенциал изделия смещается в отрицательную сторону, причем может произойти депассивация. Но поскольку иногда это происходит довольно медленно, простая автоматика может обеспечить включение и выключение защитного тока в нужное время. Когда потенциал дойдет до величины φ nn ", т.е. до начала перепассивации, ток выключается; когда потенциал сдвинется в отрицательную сторону до φ nn (начало активации), ток снова включается. Смещение потенциала в катодную сторону происходит тем медленнее, чем меньше φ nn . Чем ближе был потенциал к величине φ nn ", тем медленнее он смещается в отрицательную сторону (в направлении φ nn) при выключении тока. Например, для хрома в 0,1н. растворе Н 2 SО 4 при 75°С, если выключение тока произошло при φ =0,35в, активация наступит через 2 ч; выключение тока при φ =0,6в вызывает активацию через 5 ч; выключение же при φ =1,05в увеличивает срок начала активации более чем до 127 ч. Столь большое время, необходимое для депассивации, позволяет делать значительные перерывы в подаче тока. Тогда одной и той же установкой можно обслужить несколько объектов. Зависимость времени запассивации от потенциала включения легко объяснима при помощи концепции фазового окисла (образуется более толстый слой окисла, растворение которого требует больше времени). Труднее объяснить это явление десорбцией пассивирующего кислорода. Конечно, с ростом положительного значения потенциалапрочность связи в адсорбционном слое должна увеличиваться. Но при включении тока разряд двойного слоя происходит сравнительно быстро, хотя адсорбционный слой, возможно, сохраняется долго. 3. Если область пассивного состояния (Δφ nn) мала, то необходимо применение потенциостата, поддерживающего заданную величину потенциала (относительно некоторого электрода сравнения) в узких границах. Потенциостат должен быть способен давать большую силу тока. В настоящее время уже имеется ряд установок для анодной защиты, осуществленных в промышленном масштабе. Защищаются изделия и из обычной углеродистой стали. При анодной защите не только увеличивается срок службы аппаратуры, но также уменьшается загрязнение агрессивной среды продуктами коррозии. Например, в олеуме углеродистая сталь корродирует очень медленно и в этом смысле не нуждается в защите. Но в сосудах для хранения этого продукта происходит загрязнение его железом. Так, без анодной защиты в одной из промышленных установок содержание железа в олеуме составляло ~ 0,12 %. После наложения защиты концентрация железа снизилась до ~ 0,004 %, что соответствует его содержанию в исходном продукте. Загрязнение продуктов химической промышленности примесями соединений металлов, являющееся следствием коррозии аппаратуры, во многих случаях весьма нежелательно и даже недопустимо. Однако, использование анодной защиты связано со значительными трудностями. В то время как катодная защита может употребляться для защиты многих металлов, погруженных в любую электропроводящую среду, например твердую или жидкую, анодная защита применяется только для защиты целых секций химических установок, которые изготовлены из металла, способного пассивироваться в рабочей среде. Именно это и ограничивает ее применение. Кроме того, анодная защита потенциально опасна, поскольку при перерывах подачи тока без немедленного восстановления защиты на рассматриваемом участке начнется очень быстрое растворение, так как разрыв в пленке образует путь с низким сопротивлением в условиях анодной поляризации металла. Использование анодной защиты требует тщательного проектирования химической установки. Последняя должна иметь такую систему контроля, чтобы любая потеря защиты немедленно привлекала внимание оператора. Для этого может быть достаточным только локальное повышение анодного тока, однако в наихудшем случае может потребоваться немедленное опорожнение всей установки. Анодная защита не обеспечивает стойкости в присутствии агрессивных ионов. Так, хлоридные ионы разрушают пассивную пленку, а потому их концентрация должна поддерживаться низкой, за исключением защиты титана, который может пассивироваться в хлористоводородной кислоте. В условиях анодной защиты имеет место хорошая рассеивающая способность электролитов и поэтому для поддержания ее установленнойзащиты требуется сравнительно небольшое количество электродов. Однако при проектировании установок анодной защиты следует учитывать, что в условиях, предшествующих пассивации, рассеивающая способность хуже. Анодная защита потребляет очень мало энергии и может применяться для защиты обычных конструкционных металлов, способных пассивироваться, например углеродистой и нержавеющей стали, во многих средах. Эта защита легко подвергается контролю и измерениям и не требует дорогостоящей обработки поверхности металла, так как использует самопроизвольный эффект реакции между стенками емкостей и их содержимым. Способ изящен, и его применение, по-видимому, будет расширяться, как только будут преодолены сложности измерения и контроля.Покрытия, как метод защиты металлов от коррозии.
Защита металлов, основанная на изменение их свойств, осуществляется или специальной обработкой их поверхности, или легированием. Обработка поверхности металла с целью уменьшения коррозии проводится одним из следующих способов: покрытием металла поверхностными пассивирующими пленками из его трудно растворимых соединений (окислы, фосфаты, сульфаты, вольфраматы или их комбинации), созданием защитных слоев из смазок, битумов, красок, эмалей и т.п. и нанесением покрытий из других металлов, более стойких в данных конкретных условиях, чем защищаемый металл (лужение, цинкование, меднение, никелирование, хромирование, свинцование, родирование и т.д.). Защитное действие большинства поверхностных пленок можно отнести за счет вызванной ими механической изоляции металла от окружающей среды. По теории локальных элементов, их эффект следует рассматривать как результат увеличения электрического сопротивления (рис. 8). Повышение устойчивости железных и стальных изделий при покрытии их поверхности осадками других металлов обусловлено и механической изоляцией поверхности, и изменением ее электрохимических свойств. При этом может наблюдаться или смещение обратимого потенциала анодной реакции в сторону более положительных значений (покрытия медью, никелем, родием), или увеличение поляризации катодной реакции - повышение водородного перенапряжения (цинк, олово, свинец). Как следует из диаграмм, все эти изменения уменьшают скорость коррозии. Обработку поверхности металлов применяют для предохранения машин, оборудования, аппаратов и предметов домашнего обихода при временной защите в условиях транспортировки, хранения и консервации (смазка, пассивирующие пленки) и для более длительной защиты при их эксплуатации (лаки, краски, эмали, металлические покрытия). Общим недостатком этих металлов является то, что при удалении (например, вследствие износа или повреждения) поверхностного слоя скорость коррозии на поврежденном месте резко возрастает, а повторное нанесение защитного покрытия не всегда бывает возможно. В этом отношении легирование является значительно более эффективным (хотя и более дорогим) методом повышения коррозионной стойкости металлов. Примером повышения коррозийной стойкости металла легированием являются сплавы меди с золотом. Для надежной защиты меди необходимо добавлять к ней значительное количество золота (не менее 52,2 ат.%). Атомы золота механически защищают атомы меди от их взаимодействия с окружающей средой. Несравненно меньше количество легирующих компонентов требуется для повышения устойчивости металла, если эти компоненты способны образовывать с кислородом защитные пассивирующие пленки. Так, введение хрома в количестве нескольких процентов резко увеличивает коррозионную стойкостьИнгибиторы.
Скорость коррозии можно снизить также изменением свойств коррозионной среды. Это достигается или соответствующей обработкой среды, в результате которой уменьшается ее агрессивность, или введением в коррозионную среду небольших добавок специальных веществ, так называемых замедлителей или ингибиторов коррозии. Обработка среды включает в себя все способы, уменьшающие концентрацию ее компонентов, особенно опасных в коррозионном отношении. Так, например, в нейтральных солевых средах и пресной воде одним из самых агрессивных компонентов является кислород. Его удаляют деаэрацией (кипячение, дистилляция, барботаж инертного газа) или смазывают при помощи соответствующих реагентов (сульфиты, гидразин и т.п.). Уменьшение концентрации кислорода должно почти линейно снижать предельный ток его восстановления, а следовательно, и скорость коррозии металла. Агрессивность среды уменьшается также при ее подщелачивании, снижение общего содержания солей и замене более агрессивных ионов менее агрессивными. При противокоррозионной подготовке воды для уменьшения накипеобразования широко применяется ее очистка ионнообменными смолами. Ингибиторы коррозии разделяют, в зависимости от условий их применения, на жидкофазные и парофазные или летучие. Жидкофазные ингибиторы делят в свою очередь на ингибиторы коррозии в нейтральных, щелочных и кислых средах. В качестве ингибиторов для нейтральных растворов чаще всего применяются неорганические вещества анионного типа. Их тормозящее действие связано, по-видимому, или с окислением поверхности металла (нитриты, хроматы), или с образованием пленки труднорастворимого соединения между металлом, данным анионом и, возможно, кислородом (фосфаты, гидрофосфаты). Исключение представляют в этом отношении соли бензойной кислоты, ингибирующий эффект которых связан, главным образом, с адсорбционными явлениями. Все ингибиторы для нейтральных сред тормозят преимущественно анодную реакцию, смещая стационарный потенциал в положительную сторону. До настоящего времени еще не удалось найти эффективных ингибиторов коррозии металлов в щелочных растворах. Некоторым тормозящим действием обладают лишь высокомолекулярные соединения. В качестве ингибиторов кислотной коррозии применяются почти исключительно органические вещества, содержащие азот, серу или кислород в виде амино-, имино-, тиогрупп, а также в виде карбоксильных, карбонильных и некоторых других групп. Согласно наиболее распространенному мнению, действие ингибиторов кислотной коррозии связано с их адсорбцией на границе раздела металл - кислота. В результате адсорбции ингибиторов наблюдается торможение катодного и анодного процессов, снижающие скорость коррозии. Действие большинства ингибиторов кислотной коррозии усиливается при одновременном введении добавок поверхностно - активных анионов: галогенидов, сульфидов и роданидов. Парофазные ингибиторы применяются для защиты машин, аппаратов и других металлических изделий во время их эксплуатации в воздушной атмосфере, при транспортировке и хранении. Парофазные ингибиторы вводятся в конвейеры, в упаковочные материалы или помещают в непосредственной близости от работающего агрегата. Благодаря достаточно высокой упругости паров, летучие ингибиторы достигают границы раздела металл - воздух и растворяются в пленке влаги, покрывающей металл. Далее они адсорбируются из раствора на поверхности металла. Тормозящие эффекты в этом случае подобны тем, какие наблюдаются при применение жидкофозных ингибиторов. В качестве парофазных ингибиторов используют обычно амины с небольшим молекулярным весом, в которые введены соответствующие группы, например NО 2 или СО 2 . В связи с особенностями использования парофазных ингибиторов к ним предъявляются повышенные требования в отношении их токсичности. Ингибирование - сложный способ защиты, и его успешное применение в различных условиях требует широких познаний.Протекторная защита и электрозащита.
Протекторная защита применяется в тех случаях, когда защищается конструкция (подземный трубопровод, корпус судна), находящаяся в среде электролита (морская вода, подземные, почвенные воды и т. д.). Сущность такой защиты заключается в том, что конструкцию соединяют с протектором - более активным металлом, чем металл защищаемой конструкции. В качестве протектора при защите стальных изделий обычно используют магний, алюминий, цинк и их сплавы. В процессе коррозии протектор служит анодом и разрушается, тем самым предохраняя от разрушения конструкцию. По мере разрушения протекторов их заменяют новыми. На этом принципе основана и электрозащита. Конструкция, находящаяся в среде электролита, также соединяется с другим металлом (обычно куском железа, рельсом и т. п.), но через внешний источник тока. При этом защищаемую конструкцию присоединяют к катоду, а металл - к аноду источника тока. Электроны отнимаются от анода источником тока, анод (защищающий металл) разрушается, а на катоде происходит восстановление окислителя. Электрозащита имеет преимущество перед протекторной защитой! радиус действия первой около 2000 м, второй - около 50 м. Изменение состава среды. Для замедления коррозии металлических изделий в электролит вводят вещества (чаще всего органические), называемые замедлителями коррозии или ингибиторами. Они применяются в тех случаях, когда металл следует защищать от разъедания кислотами. Советские ученые создали ряд ингибиторов (препараты марок ЧМ, ПБ и др.), которые, будучи добавлены к кислоте, в сотни раз замедляют растворение (коррозию) металлов. В последние годы разработаны летучие (или атмосферные) ингибиторы. Ими пропитывают бумагу, которой оберты-вают металлические изделия. Пары ингибиторов адсорбируются на поверхности металла и образуют на ней защит-ную пленку. Ингибиторы широко применяются при химической очистке от на-кипи паровых котлов, снятии окалины с обработанных изделий, а также при хранении и перевозке соляной кислоты в стальной таре. К числу неорганических ингибиторов относятся нитриты, хроматы, фосфаты, силикаты. Механизм действия ингибиторов является предметом исследования многих химиков.Создание сплавов с антикоррозионными свойствами.
Введением в состав стали до 12% хрома получают нержавеющую сталь, устойчивую к коррозии. Добавки никеля, кобальта и меди усиливают антикоррозионные свойства стали, так как повышается склонность сплавов к пассивации. Создание сплавов с антикоррозионными свойствами- одно из важных направлений борьбы с коррозионными потерями.Цели, задачи и методы исследования
Целью данной исследовательской работы является изучение коррозии и реставрации архитектурных ценностей г. Цивильск и Ивановской сельской администрации. Исходя из цели, были поставлены следующие задачи :Проанализировать литературу по данной проблеме.
Изучить способы защиты от коррозии металлических изделий.
Провести исследование по выявлению архитектурных ценностей г. Цивильска и Ивановской сельской администрации.
Предложить способы защиты исследуемым объектам.
- Сбор и анализ теоретической информации. Поиск памятников культуры: памятников, мемориальных досок и пр. Наблюдения с целью определения материала, из которого изготовлена архитектурная ценность и возможных процессов разрушения.
Результаты исследования
Исследования архитектурных ценностей г. Цивильск и ивановской сельской администрации проводилась в период с ноября по декабрь 2005 года. В ходе экскурсии по г. Цивильск были выявлены следующие достопримечательности:- Памятник, посвященный 400-летию г. Цивильск. Памятник павшим воинам в Великой Отечественной войне. Памятник В. И. Ленину. Экспозиция перед Районным военным комиссариатом. Памятник в честь участника ВОВ жителя г. Цивильск А. Рогожкина. Памятник в честь участника ВОВ жителя г. Цивильск Силантьева. Экспозиция перед детским садом №4.
Архитектурная ценность | Внешний вид (материал, форма) | Способы защиты от коррозии |
||
проводимые | наиболее оптимальные |
|||
г. Цивильск | Памятник, посвященный 400-летию г. Цивильск | |||
Памятник В. И. Ленину | Мраморный Ленин с вытянутой рукой, покрытый краской серебристого цвета, установлен на бетонной поставке высотой около 1 метра. Общая высота композиции составляет около 2,5-3 метров. | Регулярное окрашивание памятника включая постамент краской. Однако это не спасает от механических разрушений под воздействием ветра, воды и солнца. Заметна трещина на ноге. | Необходима реставрационная работа по устранению трещины. Желательно использование специальных алкидных красок для нанесения на поверхность памятяника. | |
По своей архитектуре и материалу аналогичен памятнику Ленина. В композицию входят – солдат из мрамора, покрыт серебристой краской, расположен на бетонной подставке высотой 1 метр. Подставка обложена металлическими листами. Общая высота – около 5 метров. Рядом расположена мемориальная доска, представляющая собой длинную кирпичную стену, на которую вмонтированы оцинкованные листы с фамилиями участников ВОВ, не вернувшихся с фронта. | Окрашивание краской проводится, однако из-за большой высоты памятника нерегулярно. Коррозии не подвергается. | Необходима очистка памятника от засохших листьев и веток. | ||
Экспозиция перед Районным военным комиссариатом | Пушка, установленная на подставке из кирпича. Высота около 2 метров. Металлическая (сталь), зеленого цвета. На стволе пушки надпил глубиной 4 см. | Пушка регулярно окрашивается работниками комиссариата алкидной краской зеленого цвета, правда несколько другого оттенка, чем изначальный цвет изделия. Надпил на стволе способствует разрушению. | Возможна протекторная защита, в качестве протектора можно использовать заклепки и пластины из цинка. |
|
Памятник в честь участника ВОВ жителя г. Цивильск А. Рогожкина | На подставке из бетона мраморная плита зеленого цвета. В плиту вмонтирован барельеф из коррозионноустойчивого сплава с изображением моряка Силантьева. | Реставрация памятника не проводилась очень давно. Заметны трещины на мраморной плите. Барельеф не корродирует, однако заметны отколотые части. | Уход и своевременная замена мраморной плиты, наиболее сильно подверженной разрушениям. |
|
Памятник в честь участника ВОВ жителя г. Цивильск Силантьева | Аналогичен памятнику в честь Рогожкина. Барельеф из устойчивого сплава с изображением Силантьева закреплен на мраморной подставке в виде треугольника. | Барельеф не подвергается коррозии. | Своевременное покрытие защитными составами несущих конструкций. | |
Экспозиция перед детским садом №4. | Статуи двух пионеров с горнами. | |||
п. Опытный | Памятник павшим воинам в Великой Отечественной войне | На стене из белого кирпича расположен барельеф с изображением воюющих солдат, выкрашенный золотистой краской. | Коррозии не подвергается. Окрашивается регулярно. Заметны трещины на барельефе. | Устранение трещины. |
с. Иваново | Мемориальная доска павшим воинам в Великой Отечественной войне | |||
д. Синья-Котяки | Памятник в честь 60-летия Победы в Великой Отечественной войне (воздвигнут в июле 2004 года). | Памятник изготовлен из мраморной крошки, обложенной белым кирпичом. Надписи на мемориале выкрашены в золотисты цвет. | Коррозии практически не подвергается. Может разрушаться кирпич под действием ветра, солнца и воды. | Регулярнее подкрашивание букв, своевременная замена несущих конструкций. |
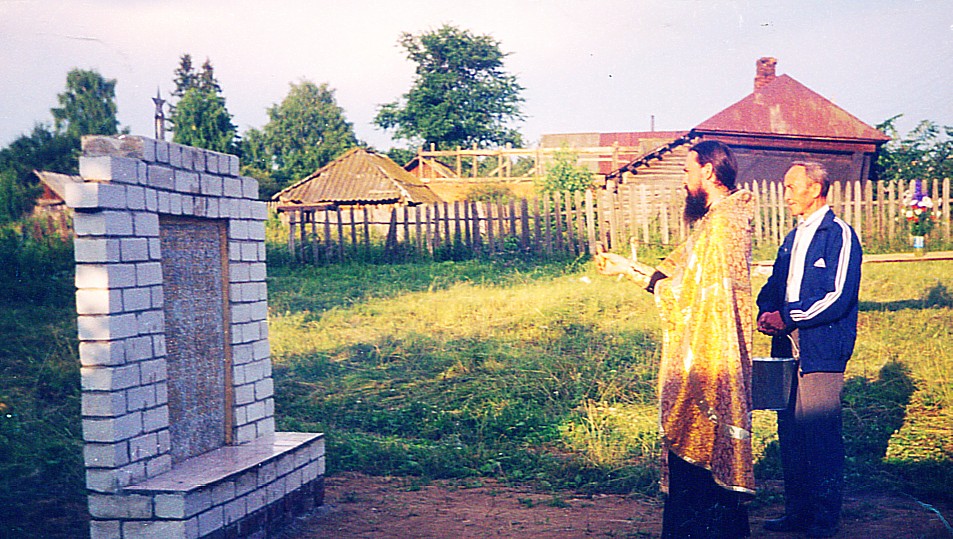
Выводы
В результате исследования архитектурных ценностей г. Цивильск и Ивановской сельской администрации мы получили важную информацию о состоянии памятников и способах их сохранения.Самопроизвольное окисление металлов, вредное для промышленной практики (уменьшающее долговечность изделий), называется коррозией. Среда, в которой металл подвергается коррозии (корродирует), называется коррозионной, или агрессивной.
Способов защиты металлов от коррозии много. Наиболее эффективными среди них являются протектирование, ингибирование, создание защитного слоя (лаки, краски, эмали) и антикоррозионный сплавов.
В г. Цивильск выявлено шесть главных достопримечательностей. Каждый исследуемый населенный пункт Ивановской сельской администрации содержит по одной архитектурной ценности, посвященной Великой Отечественной войне. В целом эти памятники представляют собой сложные композиции, изготовленные из мрамора, с добавлением металлических фрагментов. Коррозии подвергается лишь пушка перед Районным военным комиссариатом.
Для защиты от коррозии исследуемым объектам рекомендован своевременный уход и очистка, некоторым (памятник Ленину, памятник в честь павших воинов г. Цивильск) – регулярная окраска специальными составами. Памятнику в честь моряка Рогожкина требуется реставрация несущей конструкции. Для пушки, наиболее подверженной коррозии, мы предлагаем также протекторную защиту.
Список использованной литературы
- Ахметов Н.С., Общая и неорганическая химия. - М.: Высшая школа, 1989 Некрасов Б.В., Учебник общей химии. - М.: Химия, 1981 Коттон Ф., Уилкинсон Дж., Основы неорганической химии. - М.: Мир, 1979 Карапетьянц М.Х., Дракин С.И., Общая и неорганическая химия. - М.: Химия, 1993 Яковлев А. А. В мире камня. М.: Детгиз, 1991
1 От латинского соrrоdеге-разъедать.